Bearings are an important tool that helps in minimizing friction between elements that move such as in machines and equipment. It doesn’t matter whether you are an engineer, a manufacturer, or someone who wants to understand how bearings work, it is essential to get to know the different types of bearings and their functions.
In this blog, we will discuss the different types of bearings, along with their applications and how it all works together to create smooth flow in mechanical systems.
Table of Contents
What Are Bearings?
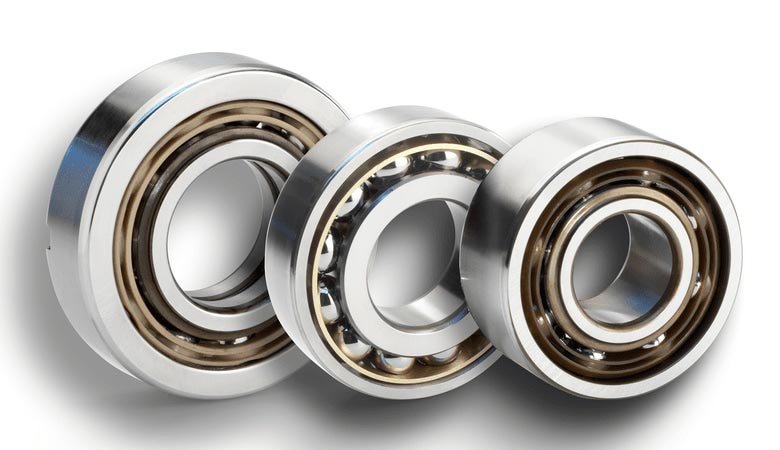
Bearings are mechanical elements that are built to support and function the movement of the parts and reduce the friction in the machines. They help by providing smooth movement, reducing damage, and increasing efficiency. Bearings are components that do not come in contact between parts, thus use less energy, have more heat retention, and improves the life of the machine.
Types of Bearings Along with Their Uses & Applications
There are many different types of bearings, each with its own characteristics that makes it suitable for specific applications.
Let’s examine the most common types of bearings and how they are commonly applied.
1. Ball Bearings
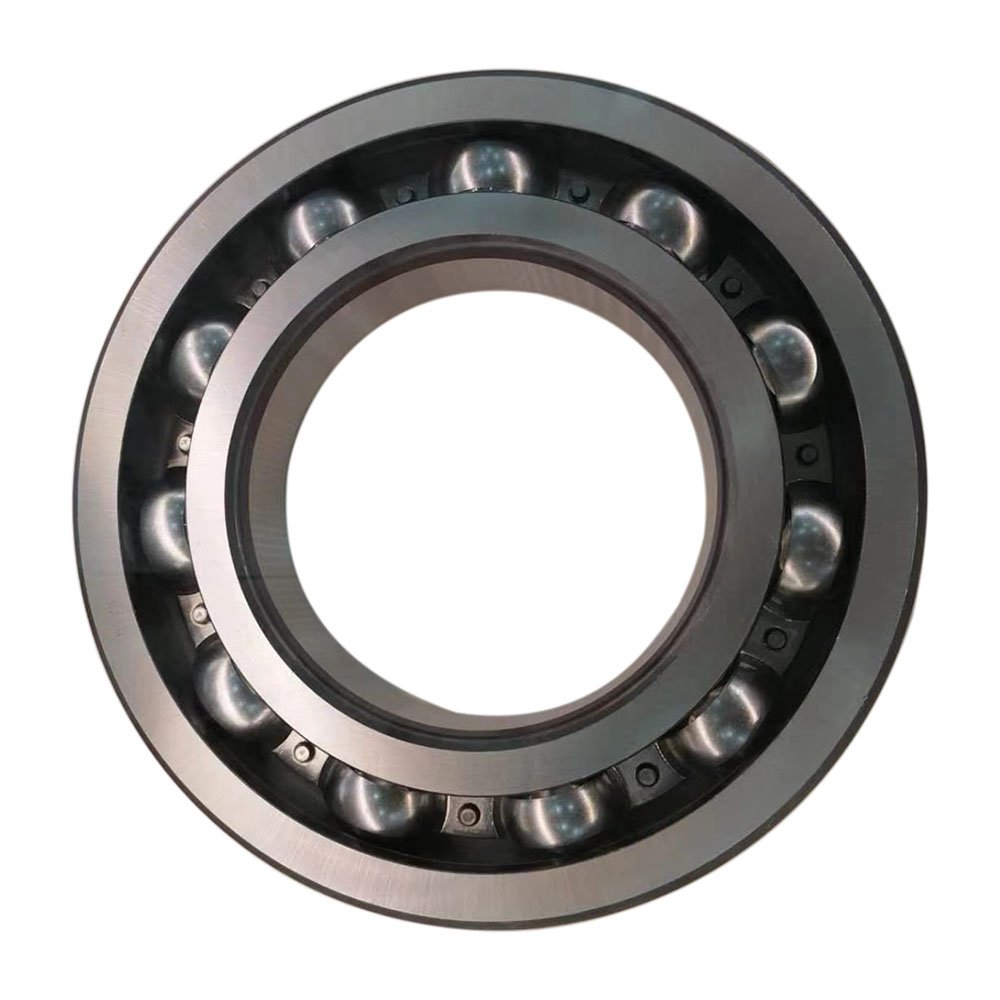
Overview
Ball bearings are arguably the most common type of bearing. They are comprised of a set of small steel balls that are situated between two metallic rings commonly called the inner and outer race. The balls will help decrease friction and allow for smooth rotational movement between two parts.
Uses and Applications
- Electric Motors: Ball bearings are also found in electric motors, both reducing the friction while allowing the motor to function properly.
- Automobiles: Ball bearings are used in car wheels, steering columns and gears.
- Computers and Electronics: In computer components such as hard-drives and cooling fans, a ball bearing will reduce friction while extending the life of the component.
2. Roller Bearings
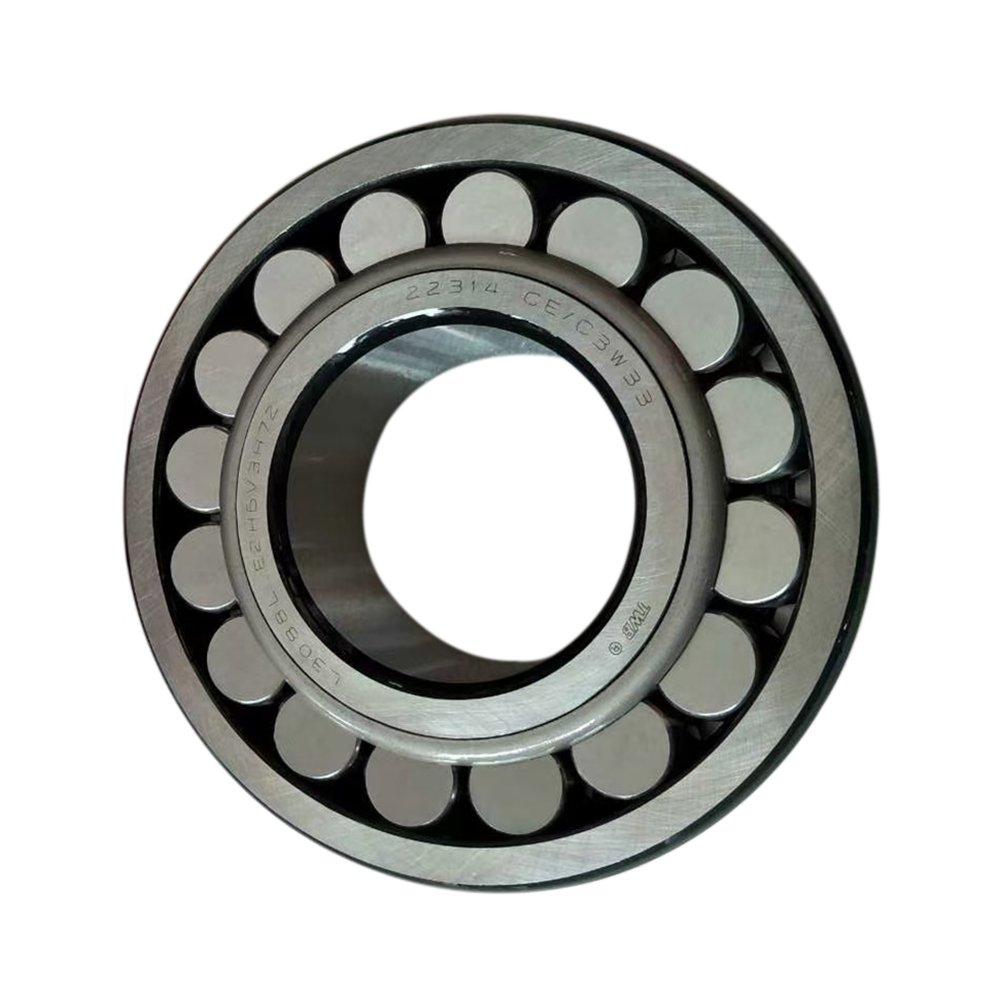
Overview
Roller bearings function in a similar manner to ball bearings, but instead of balls, they utilize cylindrical rollers to support the load. Roller bearings are able to handle larger loads than ball bearings can because the resistance is spread over a larger surface area.
Uses and Applications:
- Heavy Equipment: Roller bearings are used in heavy loading industries, for example, construction equipment, mining equipment, and industrial pumps.
- Automotive: In some car wheel hubs, roller bearings can handle larger radial loads than ball bearings.
3. Tapered Roller Bearings
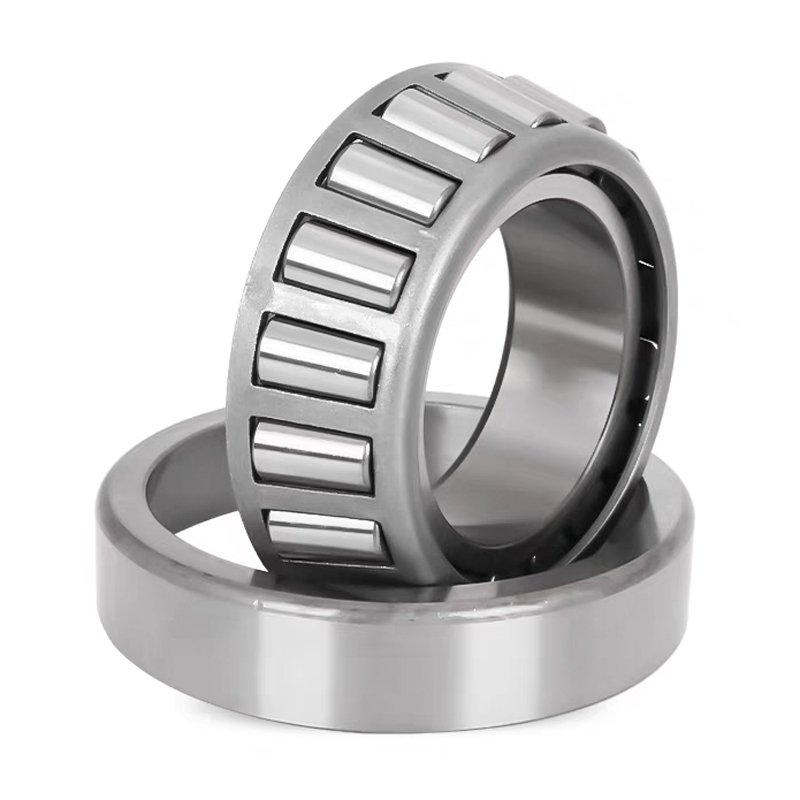
Overview
Tapered roller bearings are uniquely able to accommodate both radial and axial loads. This type of bearing is comprised of a cone-shaped roller that fits in a similar shaped matching raceway. Their special shape allows these bearings to convert both radial loads and axial loads at the same time.
Uses:
- Automotive Industry: Commonly used in car wheel hubs and transmissions, tapered roller bearings support radial and axial wheel forces.
- Mining & Construction Equipment: The heavy duty characteristic of tapered roller bearings makes them ideal for supporting large and heavy machinery in harsh environments.
4. Needle Bearings
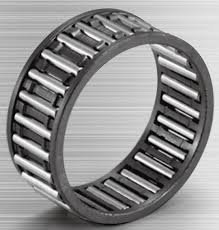
Overview
Needle bearings are a particular kind of roller bearing where the rollers are considerably longer and thinner than those in standard roller bearings. These bearings exhibit high radial loads in reduced volumes.
Uses and Applications
- Automobiles. Needle bearings are used in automotive parts like engine assemblies, transmissions, and drive shafts, where there are limitations on space.
- Industrial Machinery. Needle bearings are used in conveyor applications and gearboxes requiring compactness and load capacity.
5. Thrust Bearings
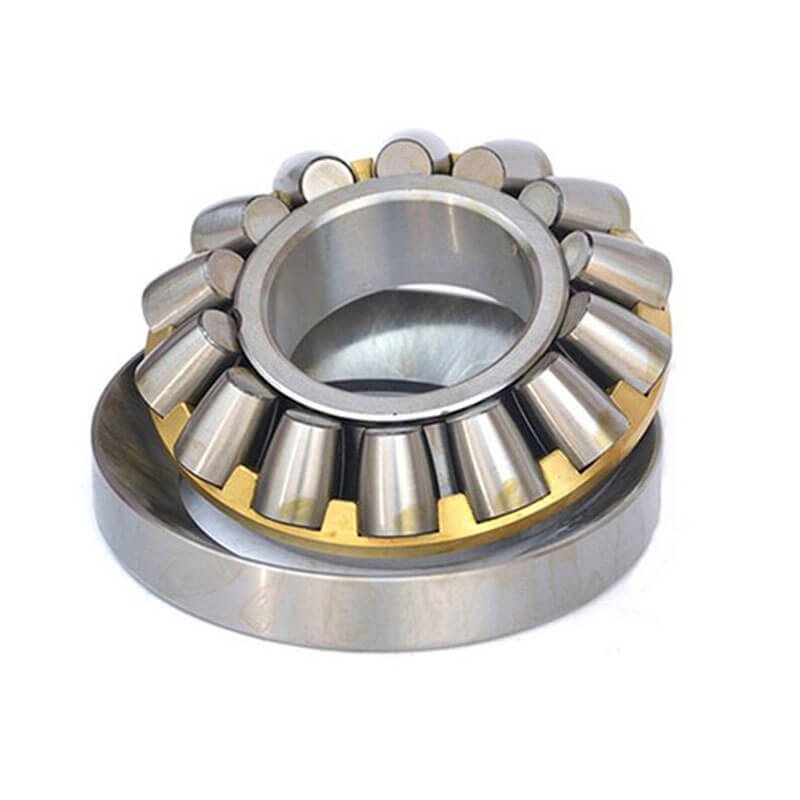
Overview
Thrust bearings are specifically built to sustain axial loads – forces that are applied along the axis of rotation. Thrust bearings contain a series of balls or rollers in an assembly between flat washers or rings. Overall, thrust bearings have many uses and applications in various industries and companies.
- Automotive Transmissions: Thrust bearings are used in automotive transmission systems in order to absorb axial loading when gear shifting occurs, which allows for smoother operation throughout.
- Machine Tools: In lathes and other machine tool applications thrust bearings will help absorb axial force generated from cutting.
6. Spherical Bearings
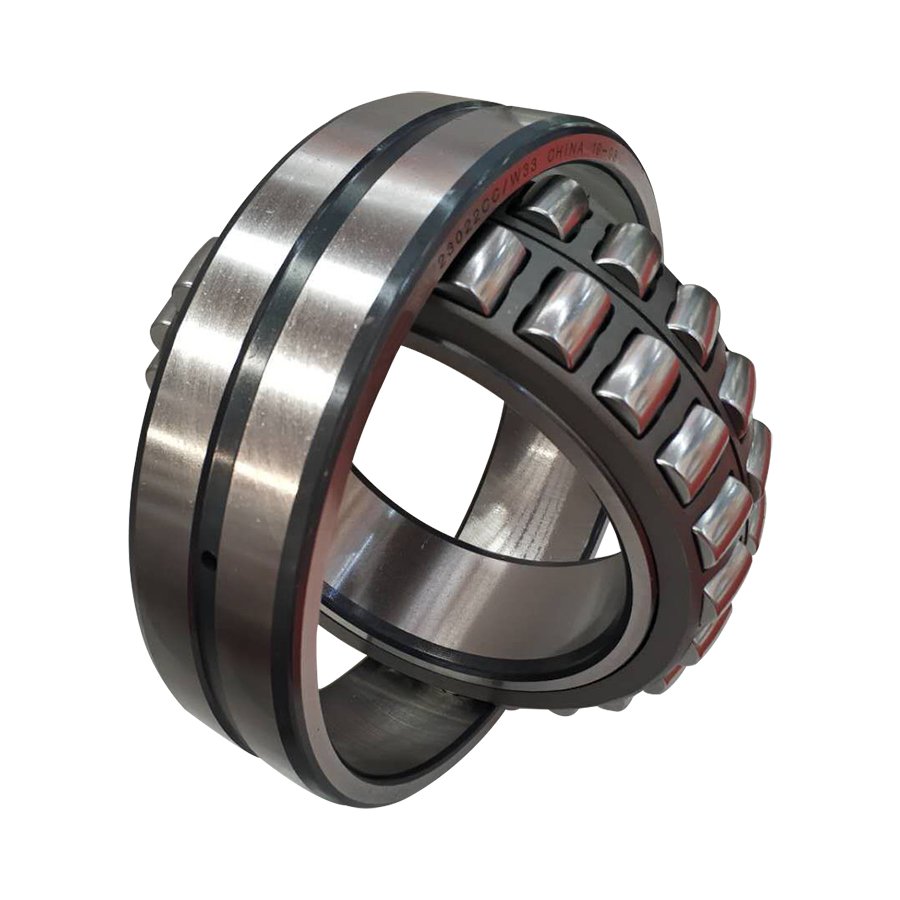
Overview
A spherical bearings inherently comprise a ball and socket configuration, meaning angular misalignment can occur between the two bearing races. Spherical bearings are perfect for applications where there may be less than perfect alignment.
Examples and Applications:
Initially, Spherical bearings were used in automotive applications, primarily suspension systems because of their ability to accommodate slight misalignment and also to make sure of smooth movement.
Until very recently it was only in special applications such as highly engineered equipment where spherical bearings would be used, however there are common applications of spherical bearings in industrial equipment like pump applications, fan applications, and compressor applications, where misalignment can enhance performance and longevity.
7. Magnetic Bearings
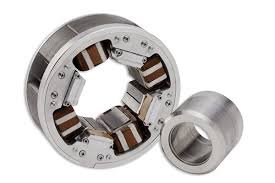
Overview
Magnetic bearings utilize magnetic fields to support the moving components without physical touch. These bearings are often used in highly niche applications where minimizing friction and wear is essential.
Common Uses and Applications
- High-Speed Rotating Machines: Magnetic bearings are frequently utilized in machines or applications that are prone to high speeds, such as turbines, flywheels, and high-speed motors that typically wear out in a hurry using traditional mechanical bearings.
- Cryogenic Equipment: Magnetic bearings are also used in cryogenic applications, such as in superconducting magnets or technologies related to space exploration, generally where standard lubricating solutions would not meet the demands of the system.
Factors to Consider When Choosing Bearings
When it comes to choosing the correct bearing for an application, a number of factors must be taken into account:
- Load: The load type (whether radial, axial, or compound) will determine the suitable bearing load.
- Speed: Bearings in high-speed applications might require unique materials or designs to minimize wear and friction.
- Environment: Bearings must be chosen appropriate for environments, including determining temperature, moisture, and other contaminants or chemicals.
- Space: Some applications are constrained for space, in which case compact bearings like needle or ball bearings are suitable.
- Cost: Each bearing type comes in varying price ranges, and price is an important consideration in mass production applications.
Conclusion
Bearings are vital parts of contemporary engineering, which is used in numerous applications and many different industries. From some of the smallest electronics to some of the largest industrial machines, just the right bearings can make all the difference in efficiency, longevity, and performance. With a bit of understanding into the types of bearings available and what they are used for, you can make appropriate choices to improve the reliability and longer-term use of the systems.
FAQs
1. How does radial load differ from axial load?
A radial load is exerted perpendicular to the rotation axis (i.e., the weight of a wheel that is rotating).An axial load is applied along the rotation axis (i.e., the force when a shaft is pushed along its length).
2. How can I determine what bearing I need?
The type of bearing you need will depend on a combination of load direction, operating speed, available space, and environmental conditions. Generally, roller bearings are appropriate for heavy loads or high speeds, and ball bearings are best for light to moderate loads.
3. What are the signs of needing to be replaced?
Signs of bearing wear are typically unusual sounds (grinding, squealing), vibration, overheating, or not rotating smoothly. Periodic maintenance and monitoring can provide an early warning of when it is time to replace a bearing.
4. How long does a bearing last?
The lifespan of a bearing depends on load, speed, lubrication, and operating conditions. Bearings can last, with good maintenance, from a few thousand rotations to several million rotations.